Factory Operations
This is the biggest area of Chasm and leads the drive to operational excellence. Our work in this area looks to ‘deliver the day’ with operations hitting the plan, before we talk about CI and fancy stuff. Automate and upskill the core workforce for using that automation. Our holy grail is your cost per unit and our holistic approach gets full clarity on how every part of your operation impacts it.
The Chasm approach to your factory operations
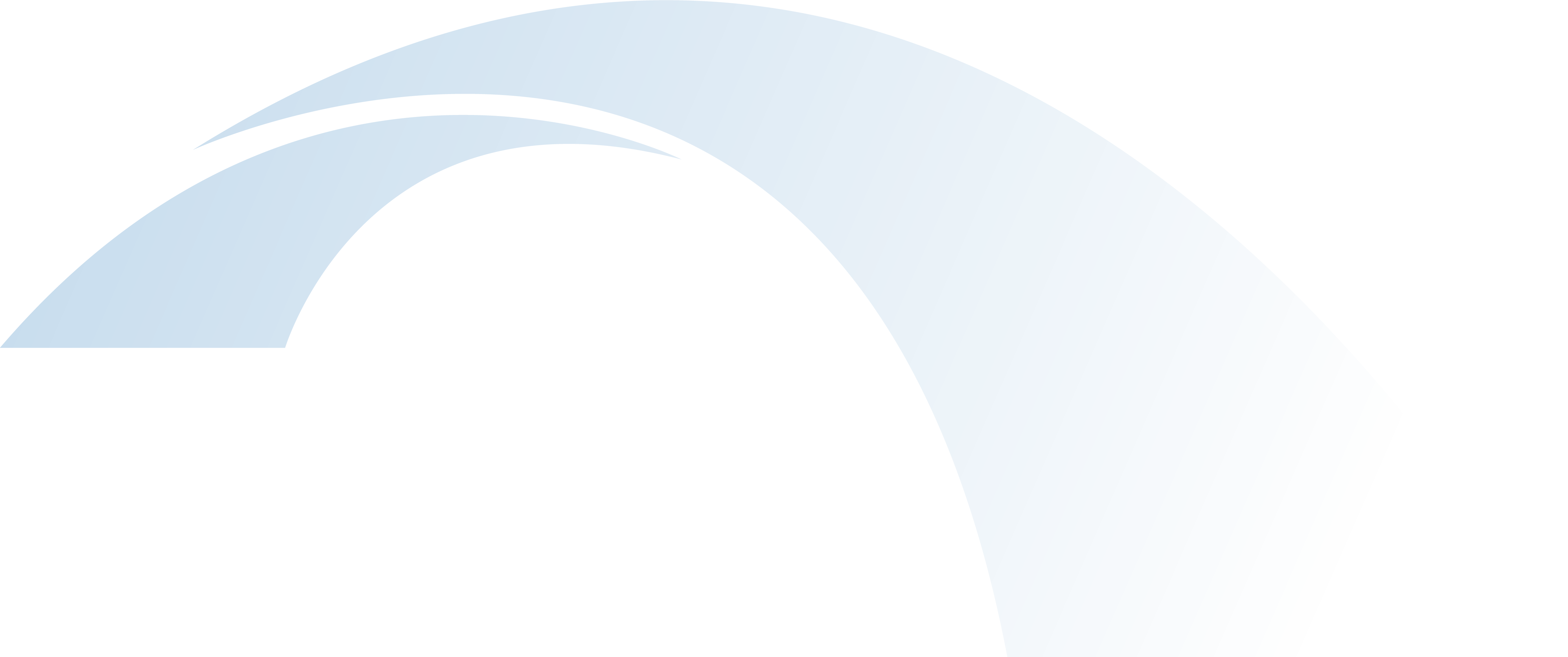
Find out more...
Health Check – We have a range of tools we use to audit an operation against a set of criteria. Depending on the site and requirements, this could be a simple checklist (mini flow RAG) to an in depth analysis.
Due Diligence (feasibility) – These are most frequently done on behalf of investors when looking at mergers, acquisitions or funding rounds.
- Is the site functionality & operationally capable?
- Is there opportunity to drive value / cost out?
- Would we combine and close sites?
A high level map of a process that will include product flow, information flow, data captured, time taken etc.
Be that simple ‘brown paper’ process maps or detailed VSM the devil is in the detail.
The idea is to ‘critique’ the process with the people who use it to identify issues and improvement options.
Common improvements include removing activities, automating tasks, speeding them up, changing the communication, better data flow & data capture.
Production efficiency is never as simple as it sounds. Ensuring all the tools, people and materials are available when needed and a production line that is capable of performing, whilst managing the daily ups and downs of a busy operation.
We perform the detailed studies and analysis to fully understand performance, by product, shift, day, manager and develop operational fixes for root cause problems.
This is how the factory works to ‘deliver the day’ (or execute the daily plan). The MCS will include a series of activities (for the various user/management level):
- Short Interval Control (SIC) – hourly check of progress against a plan, at a line / resource level, usually visually on some form of line board. (line leader level).
- Cell reviews – this is the first level of management reviewing performance probably every 2-3 hours. (line leader to area / section leader).
- Shift reviews – performance of all areas across the shift (section leaders to shift managers).
- Operations review – a daily review of yesterday in the morning and a ‘where we are’ at the end of the day. Shift manager to site manager / director (plus probably support functions).
- Site review – a weekly dashboard review of key metrics & KPIs )for all direct reports of the site director).
The MCS is the backbone of the daily operation. It is this that helps communications, information flow, actions arising, and plan delivery.
Without and MCS, you have lots of people acting down levels and running round like the proverbial headless chickens.
Our rapid development comes in many forms, be that interim support to run the operation, hands on help to deliver ongoing initiatives or an injection of horsepower when times are hard or cash is tight.
It may be a new process or system you have installed that needs 24/7 coverage, it may be ‘hands on’ support to deliver new products or production lines. This is something Chasm are renowned for.
Often sites have good plans in place for improvement but need horsepower to help create momentum and buy in with their people quickly, which is vital for the success of any project.
Where are the pinch points in your whole operation?
Do you have machines idle waiting for materials or people?
Do you have excess WIP piled up throughout the site?
Is your labour variance adverse to standard?
The finer details of product, material & labour flow are unpicked in the bottleneck line balancing analysis.
We use a series of tools developed over many years to identify opportunity, working with your people to develop improvements.
Many of these tools are in our Resources section free to download.
Do we want to reduce changeover time for increased production capability, or to allow for more changeovers thus reducing stock and working capital?
Either way the process for changeover reduction (SMED) takes a detailed look at the changeover process from end to end and will usually turn up significant benefit.
Are there too many?
Can we reduce the quantity with better planning?
Is the time taking too long and can this be reduced?
Is everyone involved in the changeover?
Good changeovers are not the result of micromanagement.
Labour control is a very difficult task, especially managing large numbers, various shifts, holidays & absence, multi-lingual workers and all teh challenges that come with people.
Whilst in simple terms it boils down to 2 questions:
- How do we control who or how many people we need on each shift and how many actually arrive?
- How do we de-crew during the shift as the numbers reduce.
In reality your are dealing with minute details and managing people.
Chasm typically manage this through a labour calculator or planning tool, connected to the factory schedules, that will pull in holidays, absence, schedules, crew requirements and agency labour to ‘calculate’ man hours required to standard.
Add in a daily labour meeting and a feedback loop to drive improvement.
As the quantity and quality of the labour market shrinks, attracting and keeping the right talent is becoming ever more difficult.
Automation is always a good way to reduce that reliance, in whatever form that may be.
Automation to remove the need for people on a certain process?
Automation of repetitive & mundane tasks to increase added value opportunity?
Whatever form that takes Chasm help with identifying automation opportunity, finding solutions with payback right through to install and operation. As we are operational experts we know what you need.
This has a multitude of things under the umbrella but will cover such things as:
- Yield loss from preparation – peeling, trimming, cutting.
- Cook losses in ovens
- Giveaway on production lines
- Floor waste
- Scrap & rework
- Rejects
- Underweights
- Disposals, out of date, FIFO stock management
As material costs are usually 60-70% of your cost of sales getting these under control can have significant impact on your P&L.
After executing the plan on a daily basis, and capturing all the key information about the shift performance using some form of SFDC, we build up a data history of performance.
Using that data history to inform ‘top loss’ reasons for failure and / or identify the opportunity to improve is the first stage of the improvement cycle.
To support this, there needs to be an infrastructure for continuous improvement. How and where do we assign projects, review milestones, support actions and provide training in the basic tools for problem solving.
Chasm create the improvement system and develop the process for delivery by defining project selection; who will do it, project charters, reviews of activity, and training required in key problem solving tools.
Once you have the fundamentals in place to ‘deliver the day’ and a basic CI structure, Chasm can add some excellence. There are a plethora of ‘tools’ we can use, but essentially most business try to ‘do lean’ before they have basics in place which is:
- Standard work – how do we standardise all roles and tasks and align to roles, responsibilities and competencies.
- We are looking for very mechanical clockwork operations. At 06:00 you greet your team, at 06:15 you walk the lines, at 06:30 you review the daily plans, at 07:00 you do first hour SIC, etc etc.
Common tools we then bring into play include:
- Changeover reduction (SMED) – structured exercises to reduce changeover times
- 5S – a structured approach to workplace organisation
- Six Sigma – process capability improvement process
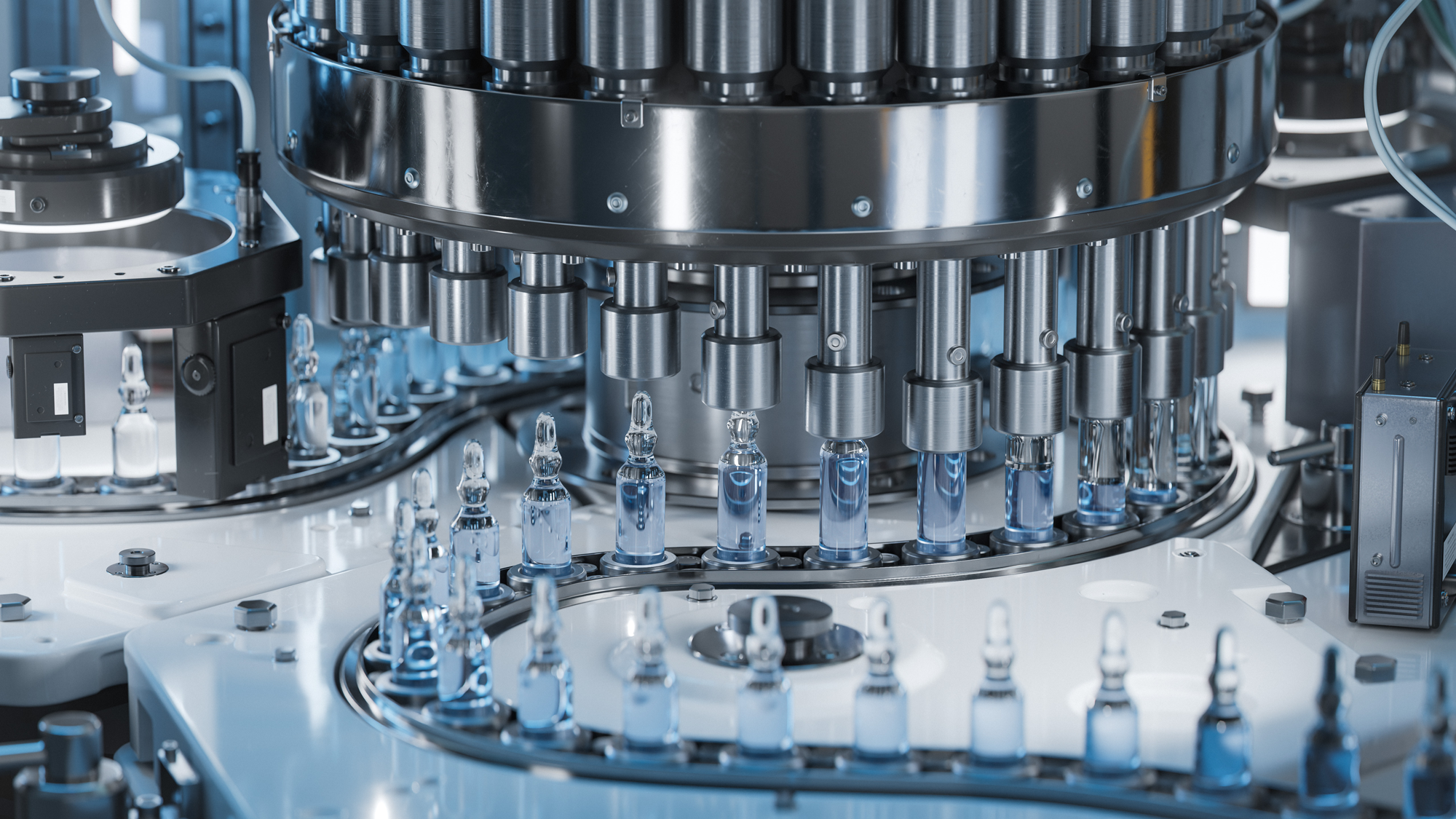
We've got some great FREE resources
Whatever support you need right now we have some resources available to download..
Case studies of previous work, useful diagnostic tools for people and processes or some self score audits of performance. Head over to the download section and have a browse.