Lean & Six Sigma
Lean is more a mindset than it is tools. It's a way of life, a strategy, behaviours and a system of thinking. Implementing tools alone will not make you Lean. Your Lean journey will be different to others, one size definitely does not fit all. From strategy to implementation to the people involved, Chasm should be your partner of choice.
The Chasm approach to your Lean Manufacturing & Six Sigma requirements
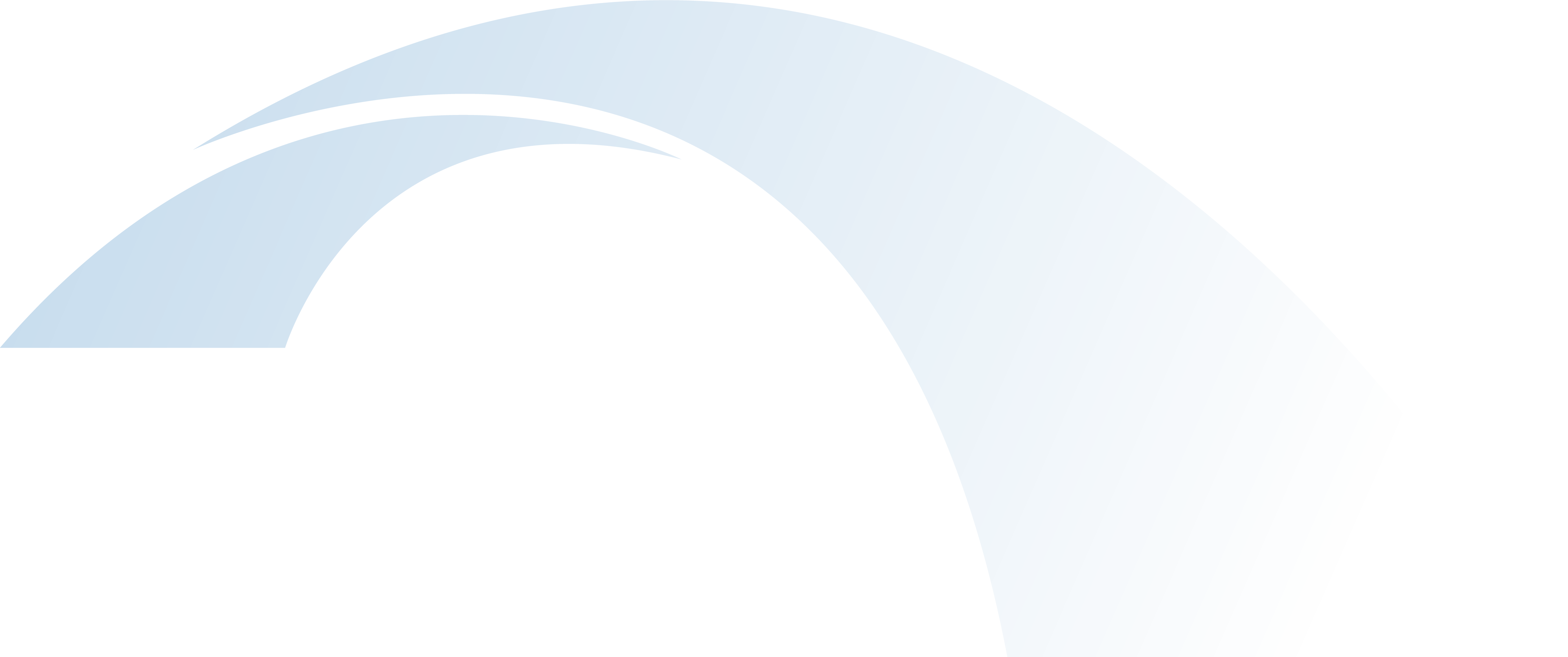
Find out more...
Click the links below to find out more of what Chasm do and how we help on your Lean journey…
The bedrock to a successful Lean Implementation is alignment of the strategic aims of the business with both the processes and people that perform daily tasks.
These cannot be done in isolation, there has to be a systematic approach to implementing change for the whole to improve.
The Lean Strategy will be intrinsically linked to the overall business strategy and the 2 are woven together during the Hoshin Kanri / Policy deployment in the early stages.
‘Hoshin Kanri, also known as policy deployment, is a systematic process for tackling long-term strategic goals through day-to-day operations, built-in review processes, and training activities that support continuous improvement’
Once the policy has been agreed and communicated there is a well-trodden path to execution.
- Identify value streams and where value is created
- Build ‘standard work’ for all tasks
- Design the optimum production flows (specific to your product)
- Develop Pull production systems (streamline flow and minimise WIP)
- Employee led Continuous Improvement (CI)
On the face of it, strategic development, Hoshin Kanri, policy deployment are quite straight forward. Keeping the focus and detail as you try to write it all down and communicate the vision clearly requires a level of experience and ‘been there, done that’.
Chasm have and bought t-shirt.
- Establish your organizational vision. Identify your organization’s key mission, vision, and values. …
- Develop strategic objectives. …
- Develop annual objectives. …
- Cascade goals throughout the organization. …
- Execute annual objectives. …
- Implement monthly reviews. …
- Conduct annual reviews.
There are a variety of tool we use to understand process flow(s) and depending on the complexity of the process, the needs of the customer, or the level of understanding required will use the relevant tool for the job.
Process Stapling: involves spending time in the workplace seeing how things are done. The most basic level of process understanding will (usually) involve the use of post it notes or actual copies of paperwork to model the flow.
Follow up activity will involve a critique of the process to determine what, if any, changes could be made to the process.
At it’s basic level there will be very little in terms if step timings or Value Added measurement, more so an understanding that changes will make it better.
Process Mapping: a more detailed exercise that will be visually represented with a flow chart using start / stop, process steps and decision boxes. The process map will have significantly more detail in terms of value added activity, and process timings such that balanced decisions can be made on the impact of any changes.
As well as the initial ‘Brown Paper’ process maps, we will develop a ‘White Paper’ to-be process as a guide for the future. Actions and activity will be geared around the White Paper requirements.
Value Stream Mapping (VSM): is a diagram of every step involved in the material and information flows needed to bring a product from order to delivery. It is a fundamental tool used in continuous improvement to identify and eliminate waste.
Like those above the VSM will have a current & future state version. VSM is a very specific tool with set criteria for how it looks and is built. It is very rare that the VSM version will tell you much more about your process than those above but it looks nicer.
At Chasm we believe in keeping things simple where possible, it’s your process so choose your map. So long as it is detailed and does the intended job who really cares?
The aim of the process map is to fully understand how things work in your organisation, what is the level of Value Added (VA) activity, and what improvements can be made to reduce waste.
Many of the tools used in operational analysis are those discussed in the ‘Factory Operations’ section of the website, but is a summary….
Time & Motion: the classic direct and continuous observation of a task with stopwatch and clipboard. Whilst the term is not used extensively these days, the methods used remain common to analysis;
Direct Observational Time Study (DOTS): does exactly what it says on the tin. A process based observation of an operator carrying out a predetermined task to understand throughput, pace, Takt time or any other key information.
Activity sample / Ratio Delay: quite often used as a ‘point in time’ assessment of work, usually in a non linear process (e.g. a warehouse). An activity sample will be taken at regular intervals (10 or 15 minutes) and simply monitor people working or idle. Whilst the outputs are less scientific it gives a good indication labour efficiency in these environments.
Line Study: a very simple tool to monitor a production line (or machine) for an extended period of time to understand true performance. Quite often there will be a quoted efficiency, the line study is a method to validate that but also understand losses.
DILO: a Day In The Life Of study quite literally you spend a full day with a person to see what they actually do. Very effective for supervisory and middle management where the actual daily activity will be very different to what they should or would like to be doing.
Pareto Analysis: a simple rule that states 80% of problems will be caused by 20% of the issues, thus addressing a small issue could have huge impact.
Brainstorm & Mind Maps: a simple creative thinking technique for generating ideas and problem solving. Usually performed as a group to bounce ideas and expand creative thinking.
Fishbone diagrams: the traditional ’cause and effect’ diagram and often a better visual representation of the brainstorm session. Typically using 6 categories for grouping causation (man, machine, method, materials, measurement, mother nature) and their associated impact on the effect.
5 Whys: is an interrogative technique to explore cause and effect, with a simple premise that asking Why? 5 times will reveal the cause of the problem. In reality it is not always 5 and changes to the questioning may give better thoughts.
PDCA: the Plan-Do-Check-Act cycle is an iterative method for the management of continuous improvement activities.
SPC: is the use of statistical methods to monitor and control the quality of production processes. Usually plotting the output of that process on a control chart gives a clear indication if a process starts to deviate. This in turn promotes early detection of potential issues and allows for corrective action prior to the creation of waste.
5s: is a 5 step methodology for workplace organisation. 5s is the bedrock to any Lean program and the first opportunity to determine the behavioural aspects of a change program.
SMED: Single Minute Exchange of Dies or Changeover reduction is a tool used to dramatically reduce the time it takes to complete equipment changeovers. Traditionally the single-minute refers to changeovers less than 10 minutes and used by Toyota to allow more changeovers and reduce WIP. Typically now used as a tool to generate more operating time and promote efficiency.
Line Balancing: line balancing is a tool used for balancing operator and machine time to match the production rate to the takt time.
Standard work: is a concept that involves finding the best method for completing a task and making that the standard. The SWI will include clear and detailed guidance on execution of the task and will often be written in conjunction with the people performing the task. As well as providing the ‘standard’ for all tasks they aid training new people and form the basis of any subsequent measure of compliance.
Takt: Takt Time is the rate at which parts or products must be produced in order to meet customer demand. For a given production line, if production time is exactly equal to takt time, then the line is perfectly balanced. Otherwise, resources should be reallocated or rearranged to remove bottlenecks or excess capacity. In other words, the quantities of workers and machines assigned to each task in the line should be rebalanced to meet the optimal production rate.
Bottleneck analysis: bottlenecks are the slowest or restrictive parts of a system or process that impacts productivity. In a factory this will be a machine, person or department that slows the rate of output of a given process. Understanding bottlenecks and how to overcome them will make the operation more productive.
JIT: just-in-time, or JIT, inventory system is a strategy in which orders of raw materials for manufacturing are aligned closely with production schedules.
In a JIT system, companies keep on hand only materials that will be immediately used for the production of products, dramatically reducing stock holding costs and cash flow.
Kanban: is a material scheduling and control process for lean manufacturing and Just-In-Time (JIT) using visual methods to show where stock is needed. A key part of the pull production process Kanban ensures stocks are only replenished when needed at a rate that corresponds to the beat of the process. Often using card systems or point of use boxes, the card or empty box indicates the requirement to replenish.
Andon: is a system that alerts the relevant people to a process or quality issues. Either a cord or button on the production line that allows an operator to stop the line if a defect is found such that corrective action can be taken. Common reasons for activation of the Andon are; Parts Shortage, defects, malfunction or safety issues.
1 Piece flow: One Piece Flow, also known as Single Piece Flow or Continuous Flow, is a base concept in Lean Manufacturing and Lean Six Sigma. It refers to the practice of moving one workpiece at a time between operations within a production process, rather than batching work. Aligned to line balancing and Takt one piece flow ensures the rate of production matches the rate of demand.
Kaizen: is a strategy where employees at all levels of a company work together proactively to achieve regular, incremental improvements to the manufacturing process. In a sense, it combines the collective talents within a company to create a powerful engine for improvement. Kaizen is also referred to as Continuous Improvement.
OEE: Overall Equipment Effectiveness is a standard for measuring manufacturing productivity and gives a percentage score to measure this performance. Mathematically it uses 3 performance measures multiplied to attain that percentage score (A x P x Q)
Availability: the amount of time as a percentage the machine is planned to run from a given base (168 hours
Performance: how much of that operating time the machine ran at full speed
Quality: the percentage of good quality parts from total output
identifying the causes for lower than 100% in any category will highlight areas of opportunity to improve performance. This will include things such as unplanned time, changeovers, downtime, slow running, poor quality to name a few.
Heijunka: production levelling or smoothing, Heijunka is a technique for reducing unevenness which in turn produces waste. It’s primary aim is to produce items at a constant rate so up and down stream steps can work at predictable rates.
Poka Yoke: also Error Proofing is the implementation of a mechanism in a process that prevents, corrects or makes any error immediately visible. It is a means to de-skill the need for operators to perform quality checks having a built in process for doing so. For example height bars or a to stop oversized pieces, metal detectors in-line in food manufacturing, USB sticks that only fit one way.
Jidoka: is a manufacturing concept that seeks to improve quality control by incorporating human intelligence into automated processes. “Jidoka” is a combination of two Japanese words: “jidou” (automation) and “kaizen” (meaning improvement). Jidoka is an important part of lean manufacturing, continuous improvement, and waste reduction.
Jidoka is fundamentally about incorporating quality into the manufacturing process rather than relying on inspection and rework to correct defects. Jidoka frees workers up to focus on higher-level tasks like problem-solving and process improvement by automating repetitive tasks and using machines to monitor production.
Gemba: is a Japanese word meaning “the actual place.” In lean the gemba refers to “the place where value is created,” such as the shop floor in manufacturing, the operating room in a hospital, the job site on a construction project, the kitchen of a restaurant, and the workstation of a software programmer.
The term “going to the gemba” is described by the Japanese term “genchi gembutsu”
A popular approach in companies who implement lean principles is called “Gemba Walks,” which denote the action of going to see the actual process, understand the work, ask questions, and learning from those who do the work. It is an opportunity for management and support staff to break away from their day-to-day tasks to walk the floor of their workplace to identify wasteful activities. The objective is to understand the value stream and its problems, rather than review results or make superficial comments from their office or conference room.
TPM: Total Productive Maintenance is a holistic approach to equipment maintenance that emphasises proactive and preventative maintenance over reactive. It works on a shared approach to maintenance with basic tasks undertaken by operators, leaving skilled engineers time for higher complex activities. The aim is to ensure machines never stop through unforeseen breakdowns, improving efficiency and reliability.
Six Sigma is a set of techniques and tools for process improvement. It was introduced by American engineer Bill Smith while working at Motorola in 1986.
Six Sigma strategies seek to improve manufacturing quality by identifying and removing the causes of defects and minimizing variability in manufacturing and business processes. This is done by using empirical and statistical quality management methods and by hiring people who serve as Six Sigma experts. Each Six Sigma project follows a defined methodology and has specific value targets, such as reducing pollution or increasing customer satisfaction.
The term Six Sigma originates from statistical quality control, a reference to the fraction of a normal curve that lies within six standard deviations of the mean, used to represent a defect rate.
The Six Sigma process follows a structured 5 stage (DMAIC) approach to improvement.
- Define the system, the voice of the customer and their requirements, and the project goals, specifically.
- Measure key aspects of the current process and collect relevant data; calculate the “as-is” process capability
- Analyse the data to investigate and verify cause and effect. Determine what the relationships are and attempt to ensure that all factors have been considered. Seek out the root cause of the defect under investigation.
- Improve or optimize the current process based upon data analysis using techniques such as design of experiments, poka yoke or mistake proofing, and standard work to create a new, future state process. Set up pilot runs to establish process capability.
- Control the future state process to ensure that any deviations from the target are corrected before they result in defects. Implement control systems such as statistical process control, production boards, visual workplaces, and continuously monitor the process. This process is repeated until the desired quality level is obtained.
Many of the tools used in Lean are also present in Six Sigma projects though the emphasis is on statistical analysis of measurements and control of process variation.
Chasm run a variety of ILM certified and recognised Six Sigma courses. Operating at both Yellow & Green belt levels the courses can be tailored to the specific requirements of the client(s).
Yellow Belt: run as either a 1-day ‘appreciation’ session for middle managers to understand the core concepts of Six Sigma projects, or a multi-day program where candidates get to practice tools in a safe and practical environment.
Green Belt: we have several options for delivery of the Green Belt certification;
- 3-day: is a condensed program of training delivery with minimal hands-on use of the tools
- 5-day: a longer version of the 3 day course that allows for practical use of the tools and techniques.
- Project based: we deliver the training in 6 days over an extended period (12+ weeks) and candidates will align their learnings to a ‘work based’ improvement project.
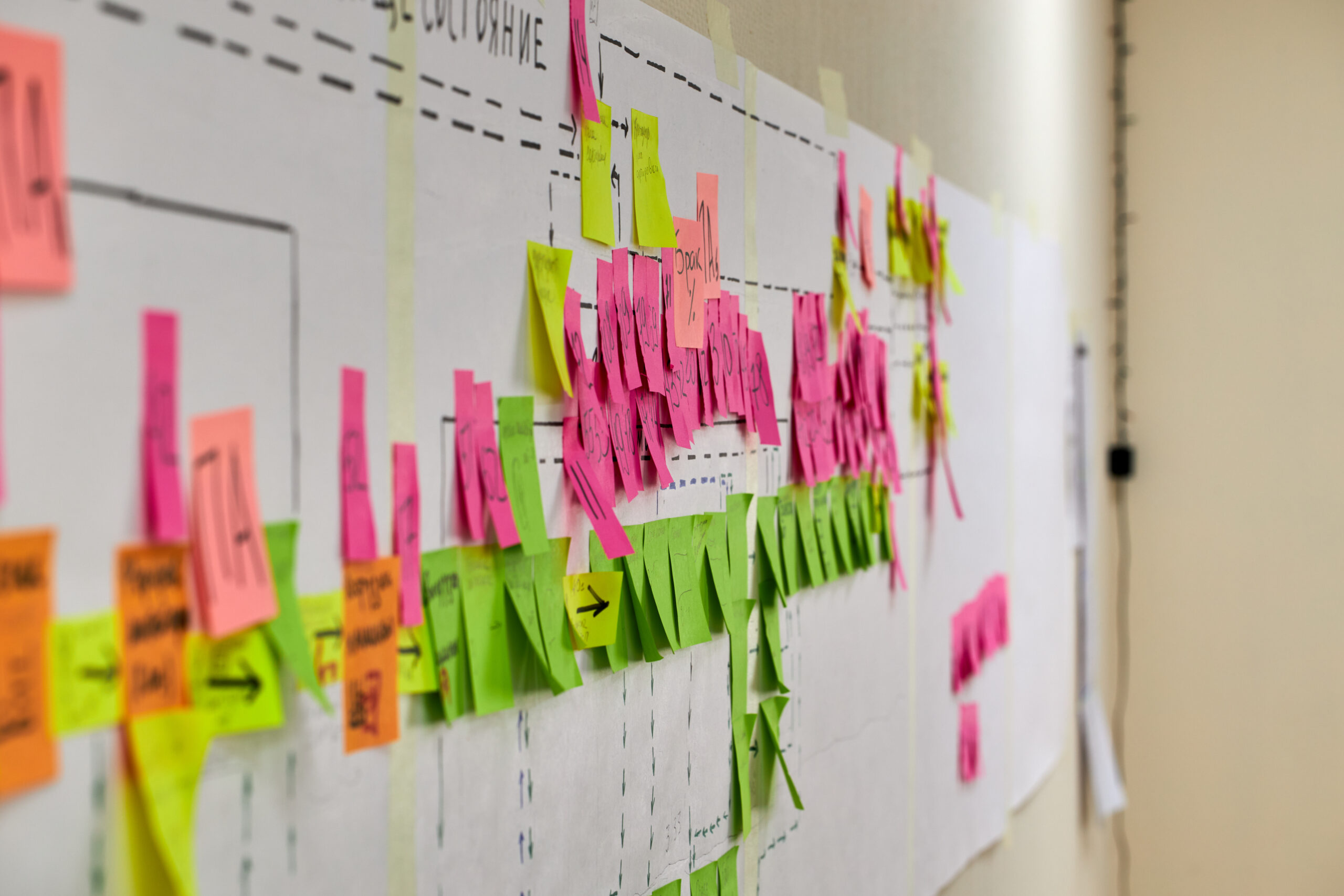
"The depth of Lean knowledge in the Chasm team is second to none.."
“We worked with Chasm on a group wide Lean implementation. From the initial kick off sessions we knew we had a winning combination. In depth knowledge, coupled with the hands on approach to developing our people at the same pace at the Lean process transformed our business….”