Business Systems
The magic that brings people and process together on a pathway to continuous improvement are the systems which Chasm build, install and operate. You get the best people using the best processes to deliver daily demand, to cost, and develop new ways of working. This is the start of your journey to excellence.
The Chasm approach to your business systems
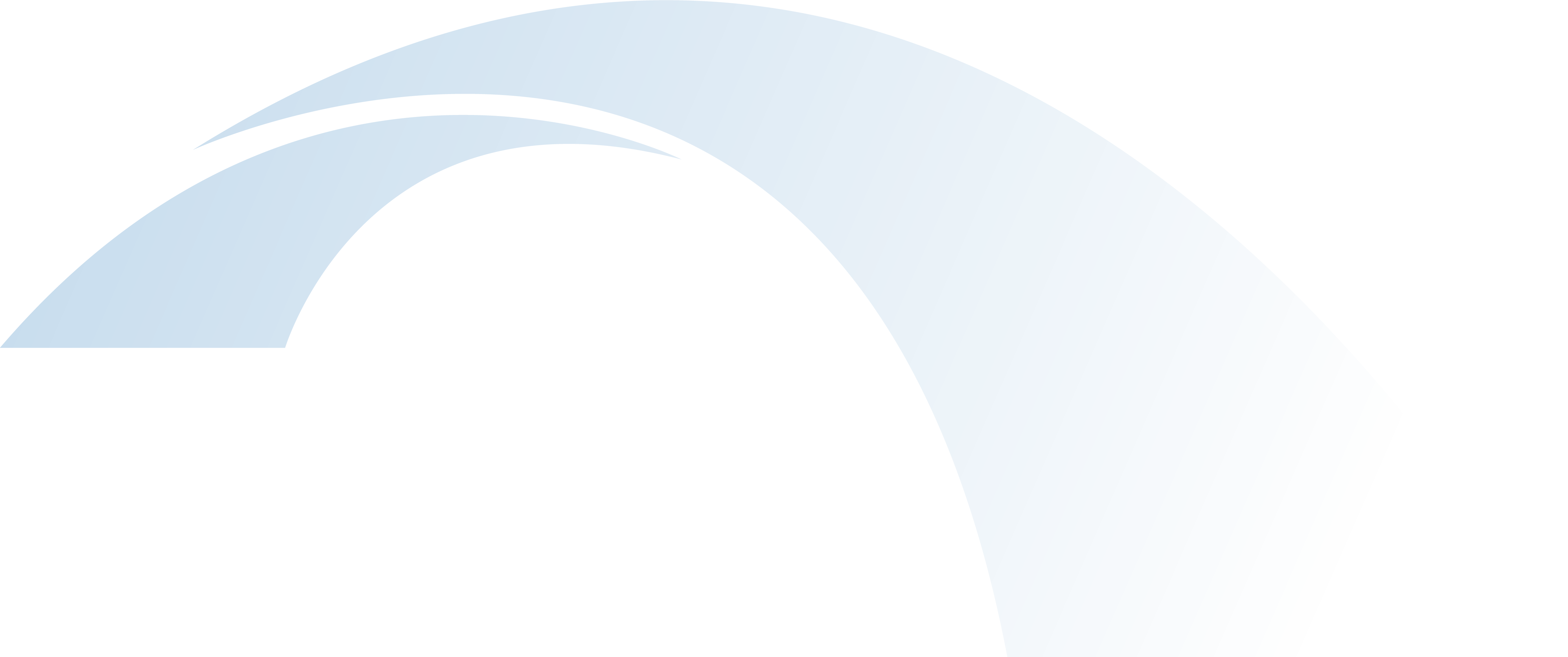
Find out more...
At the heart of most manufacturing businesses is the Enterprise Resource Planning (ERP) system. Typically these are installed by finance people and primarily used for financial information (purchase & sales ledgers, transactional postings, stock management etc) though nowadays ERP systems are much better and have greater functionality through modules to run operations also.
Typically the ERP system will have tons of ‘master data’ to support the financial operation including:
- Supplier,
- Customers,
- Bill of material,
- Price files
Each of the above will then have granular detail to help process the weekly / monthly P&L.
Whether within ERP system or as a stand alone tool there are many other business systems that are required.
Chasm either build or install off the shelf versions. Why do we build some and install others? The answer comes down to size, complexity and cost.
Smaller companies don’t have the need or money to be installing system solutions thus Chasm build versions in Excel, Access, Java or whatever format is right for you, the client
The MRP converts demand into material requirements. Typically, a business will use the MRP in 3 different ways..
- Long term demand. 3 months+ to forecast bulk requirements, maybe lay down contracts for supply and financial modelling.
- Medium terms demand. 1-12 weeks to determine what needs to be called off from suppliers to ensure it is at the factory when needed.
- Short term demand. What is needed tomorrow and how much of that do we already have inside our 4 walls. This is where WIP & floor stocks play such a vital part as they need to be included in any calculations.
A good MRP solution requires 3 key elements: demand, stock & purchases. The more accurate these are the better control of your inventory.
We usually find the quality and accuracy of stock counting is poor for 3 reasons..
- It is likely to be constantly moving in a 24/7 factory.
- It is usually counted inaccurately at night when there is less management supervision.
- There is too much of it, it’s difficult to see so they make a guess.
This just does what it says on the tin.
Many warehouses will run without a WMS and count stock each day probably into an Excel spreadsheet or a proforma count sheet and pass to accounts to make sense of it.
There are many issues in here usually around units of measure.
- Do we count labels in eaches or 1000s?
- We buy in KG but count in bags (there may be 15kg in a bag) etc.
A decent WMS implemented well with transactional disciplines will provide live stock all day every day. The level of granularity of live stock will be determined by what the clients needs and the transactions required to achieve it.
Complex operation you may need to perform multiple transactions on a product which is time consuming. Great but time consuming. Doing it with a scanner is much easier and more accurate.
A CMMS is used for asset care. Typically it will hold all the data about machines and equipment, service schedules, parts needed, times, methods etc and is used to control the preventative maintenance of machinery.
As the system is computerised you would also log non-preventative activity such as breakdowns so that the system can learn / be adapted to change preventative cycles to catch break-downs before they occur.
The system would allocate tasks to engineers based on work orders, assign spares and build a daily routine. In a site with many machines, each with many moving parts, preventative maintenance is always a key to keeping lines operational.
There is a trade off in that when a line is on maintenance it cannot be used, and typically maintenance will be the first thing to go when we are behind the plan. This begins a vicious cycle that ends up with catastrophic failure at some stage.
The data stored and captured as part of the Planned Maintenance routines improves asset care, measures MTBF, allows decisions to be made around CapEx, controls spend and holds the engineering team to account.
The demand planner converts the sales forecast into a format we can use to review capacity, determine operational requirements, feed MRP and build daily line schedules. Demand planning systems are typically lacking most manufacturing operations.
Accuracy of forecast and inclusion in a robust S&OP process is essential to the efficiency of the operation.
Depending on whether a business ‘makes to order’ or ‘makes to stock’ the granularity of the demand planner will change.
If we have a stock profile we can use as buffer for high / low orders then demand accuracy is less relevant. The obverse is true also.
This is bread and butter functionality we either build the capability in the ERP system, build something ourselves or find an off the shelf package that suits the needs of the business.
Chasm work with industry leading providers of MES & MIS systems of various size and scale to suit the needs of your business.
Finding a solution for your site is the easy part. Setting it up with key master data, developing the data structure, the granularity of data and escalations process takes considerable time and effort.
Once you have all that, embedding the process with the right disciplines and behaviours is critical to getting benefit from such systems.
We have vast experience in most popular MES / MIS solutions including
- Harford Control
- Redzone
- Lineview
- Scansys
- Sicon
and many more.
EDI in it’s traditional form is the interface between your customer ordering portal and your ERP system. Then used to send information back to your customers on the form of Invoices, Credit notes, Advanced Shipping Notices (ASNs) and much more.
Most EDI solutions now have greater functionality for communicating with your suppliers that may include Stock levels, delivery data, purchase receipts and much more. All taking significant admin out of the daily routines allowing more value added time for your team.
EDI set up is complex and most organisations only scratch the surface of the functionality of their system.
Chasm have years of experience setting up EDI systems.
Data is the lifeblood of any business, and in a world where tons of information is being captured by people and equipment all day every day what you do with that data is the key to understanding and improving performance.
Whether it is standard Power BI or bespoke data cubing analytics you are looking for Chasm have been developing solutions for many years. Not only that we know how these things work in real life, in real operations in real time so the solutions are right for you.
One of the lesser understood parts of business systems but mighty important.
Time and attendance controlled with paper sign in sheets?
Holiday planners in Excel, access control, skills matrix, return to work, absence, reward & recognition, performance reviews, disciplinary??
Pulling all these stand alone solutions into an integrated T&A, access control and HR management system is not for the faint hearted.
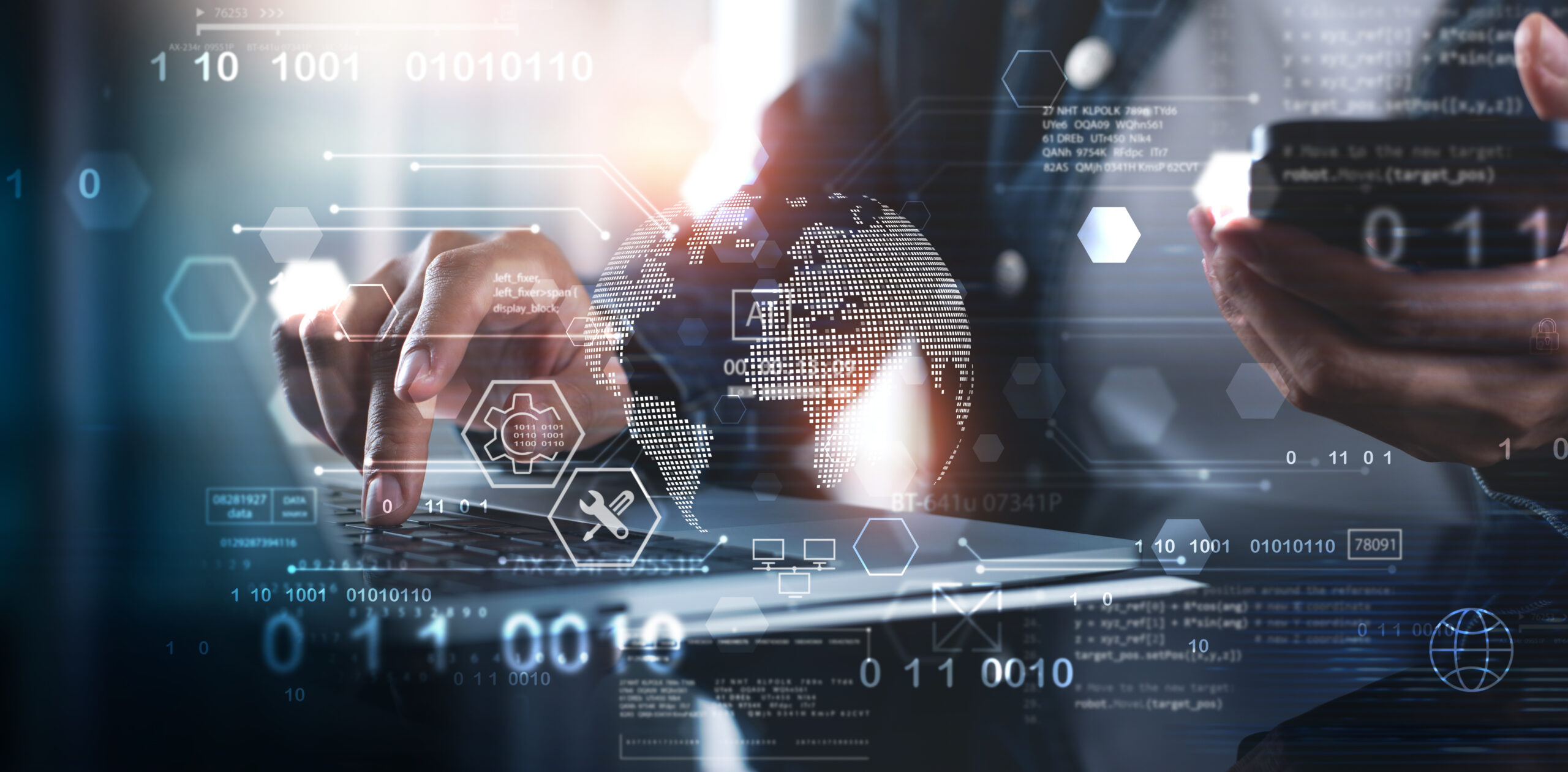
"You get the full package with Chasm"
The Chasm team are very clever and experienced in manufacturing IT and ERP systems; getting the data right whilst supporting and developing leadership and culture. You get the full package with Chasm which is just what is needed to fix a factory.
Finlay Nelson, Interim GM/Site Director
Click the button below to read more