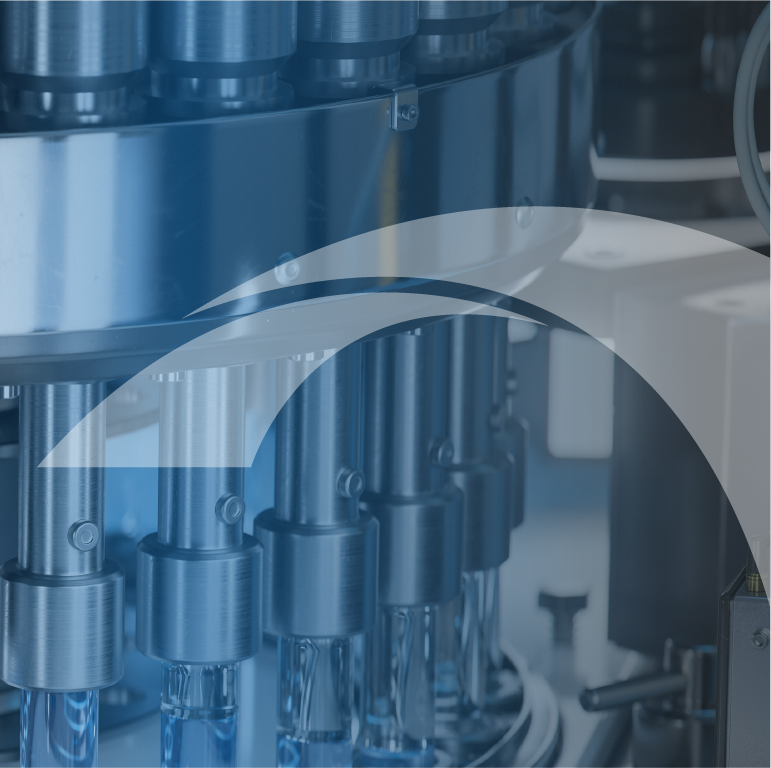
Share article:
The initial contact with most manufacturing clients is very similar. “We have a problem and wonder if you can help”?
The problem they think they have in their manufacturing operation is not always the problem they actually have and we unpick that during scoping and analysis of the factory.
But usually one of or a mix of the following is found:
🔹Material variance and waste is out of control
🔹Labour efficiency is poor
🔹We can’t get accurate data from our systems
🔹We have too many Excel tools with conflicting master data
🔹Tasks take too long as they are too manual and reliant on key people
🔹Stock accuracy is poor we need live stock that is accurate
🔹Our margins are bad, we need help improving them
The themes are common and when we start digging into your manufacturing operation there is always a mixture of process & people at the heart of the problems in your factory.
In a recent project it was 100% labour & material control. The factory was missing material standard by £6k per week, labour standard by £8k per week.
Our target was to save them £800k annualised a large part of which was needed ASAP to prevent further shareholder investment in the manufacturing site.
How we did it was a mix of ‘quick wins’, people engagement, visibility of information, process changes and lots of hand holding and 1:1 support.