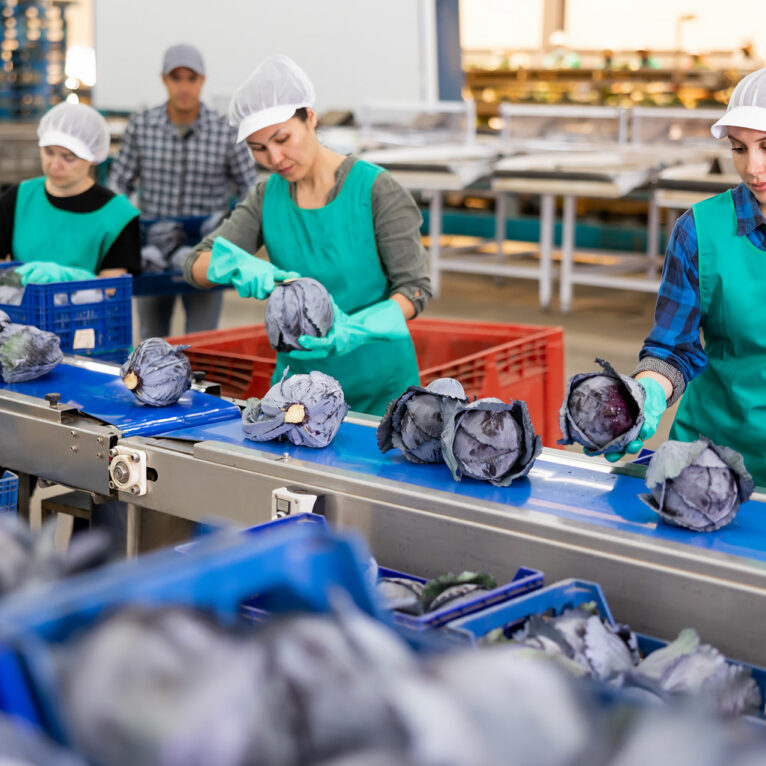
Share article:
Although I am in the vanguard of Chasm’s IT function, my background is in planning and supply chain, and for many years I was a humble factory planner and then planning manager. Ah, planners. Those poor hapless weirdos. All the blame, all the time, and none of the glory or renumeration.
So, it is with my planning experience, that I am often deployed to support our client planning function as we implement one of our excellent demand planning and scheduling systems. This is always fun, and I enjoy hearing the painful stories of being a planner in manufacturing. It always surprised me when I meet planners who are not raging alcoholics.
As I work alongside planning teams, one of the regular topics we discuss is the possibility of implementing a Fixed Repeatable Schedule (FRS). “Ah, but!” is always the response, as they reel off one hundred and ninety-nine reasons why their industry is so much different to every other. Trust me, I have heard them all before.
Even the most unstable business should be able to use some kind of FRS. Even if you’re chasing orders on a regular basis, there is always a logical sequence of doing things. A fixed repeatable schedule is just the formalisation of the logical (and efficient) sequence of making things. There can of course be rules that influence the “fixed” element of the plan, but the right order to make things rarely changes.
Creating an FRS is easier than you think. Any experienced planner, given a tiny bit of headspace, can sit and draft a “perfect plan.” It’s usually then my role to sit and flush out the rules that will be allowed to influence the most efficient sequence – and that is the key word: allowed. What are the scenarios and variables? What do we allow to trigger a plan change? This should be a wider business decision, but we often allow our planners to make these important calls. Is that right? Is it fair?
Many businesses chase a 100% service level, often without hitting it, at any cost. However, there is always a pivot-point, where changing the plan is more expensive than a short. Do you understand that fulcrum in your business? Have you ever quantified what constant plan changes cost your business in terms of inefficiency and lost capacity? You should, and Chasm can help.
The benefits of an FRS are obvious. If you have variable line crewing, you can plan de-crewing ahead of time and release heads from your operation (either for line hopping or sending expensive agency workers home). An FRS is also “signed off” by operations and planning, so we can be sure that both parties have agreed, on balance, that this is the right sequence. This logical method of planning, with a fixed sequence and an agreed ruleset, means that the plan can and should always be followed. This strengthens your plan adherence and should, with the right lines of communication, increase dialogue between operations and planning, as suggested improvements to the plan can be discussed at routine plan reviews.
It always shocks me that using FRS is so alien to many operations, or at best; they see FRS as an unobtainable aspiration. It really isn’t. Creating a robust fixed repeatable schedule, and the robust agreed ruleset to support it, is quite simple.
If you want help making sense of your plan, or your planners could benefit from one of our planning and scheduling solutions, give Chasm a call. We believe that planning is at the very centre of manufacturing, and we love making those weirdos into heroes.