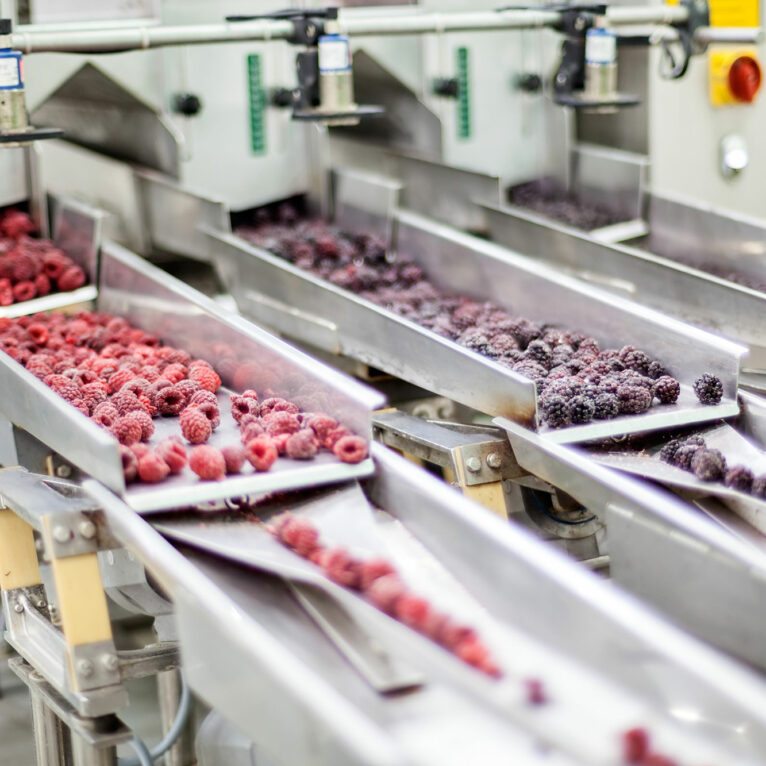
Share article:
Most manufacturing operations we are invited into have started with the control part of a continuous improvement programme but without the other key elements of a management control system (MCS). What Chasm commonly find is that they have either get lost in data that is fundamentally flawed, or worse still don’t get traction and revert back to command and control structures.
The Management Control System (MCS) is where Chasm go, we are experts in designing a MCS to kickstart your journey to operational excellence, tracking the right KPIs and getting your business on track.
The MCS is the backbone of the daily operation, facilitating communication, information flow, actions arising, and planned delivery.
Without a structured MCS you have lots of people acting down levels and running round like the proverbial headless chickens
The Management Control System (MCS) and finding your Top Loss
The first thing we need is a production plan (schedule) for every resource in the factory, based on some known standards of speed, crew, efficiency, yield etc..
Once we have a production plan we can start to manage the execution of that plan using a structured management control system (MCS) and some visual management in the factory to monitor performance by product, hour, shift, day week etc.
- One of the key basics of the MCS is making it visual so that the manufacturing team on the production lines know they have had a good day or know they need to oourse correct if they are behind plan by running through breaks, bringing on extra people, running overtime etc.
All of this MCS data needs to be captured in some form of SFDC (Shop Floor Data Capture) system so that at management level we can use it as data & information for 2 things.
- A DWOR (daily weekly operating report) to monitor site performance, understand the relationship between standards & actual performance (labour & material variances) and supply the KPIs that the overall business needs as the measure of performance
- To see the trend information of production runs, at a SKU level, so that we can start to understand:
- Why product A runs better than product B.
- Why does Product A run better on shift 1 versus shift 2.
- Why different line teams get different performance, and how they all compare to standard.
Now we have found the ‘top loss’ the continuous improvement can begin…
At this stage we need a framework for continuous improvement. Some form of meeting structure where we review top loss, agree projects, and a process for working on projects during their normal weekly jobs. Add to this some base skills and competencies in problem solving, and training in the key tools they need for both project management and problem solving.
Our job as your consultants is to build the framework, develop the tools & skills, and support the people is this new way of working.